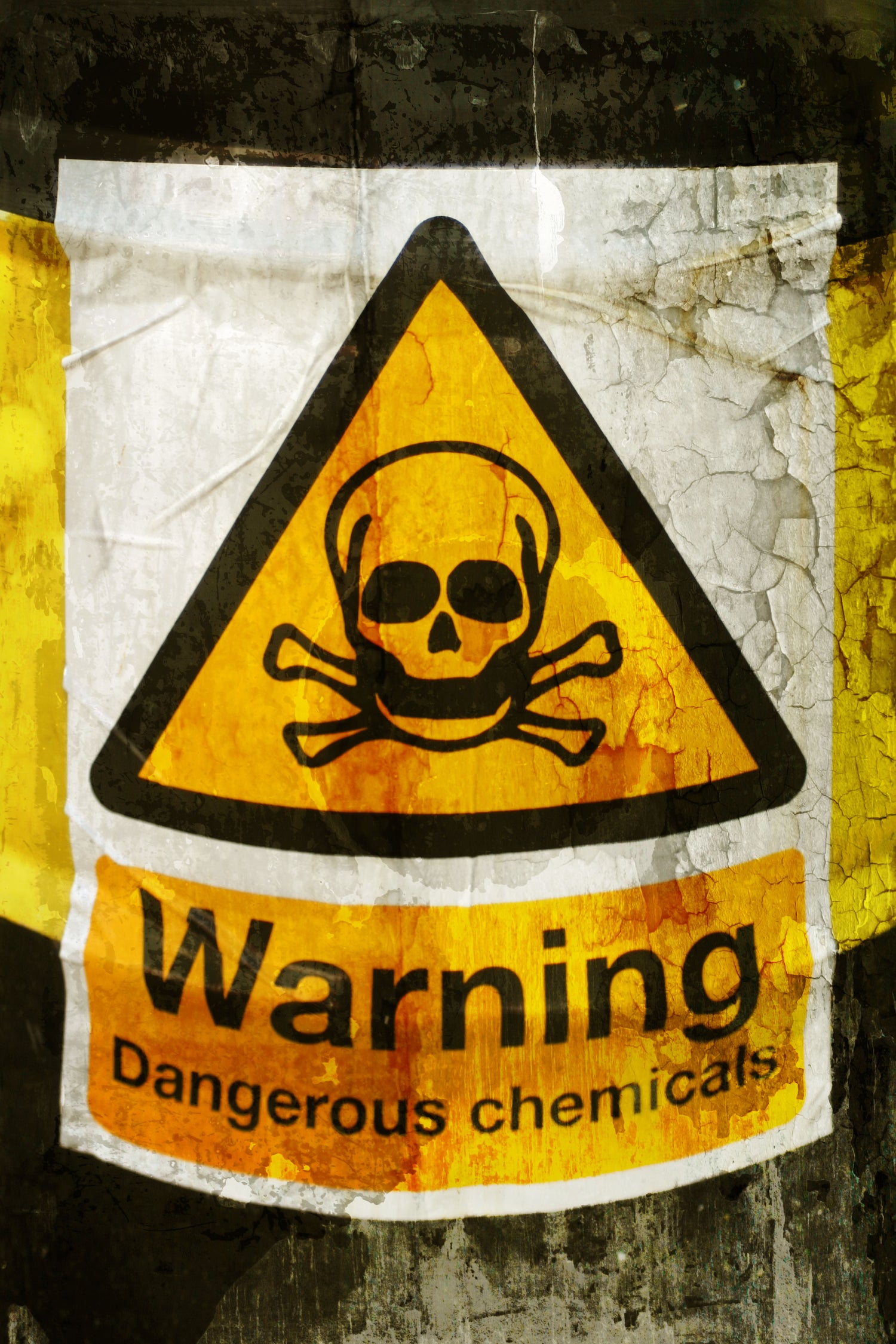
THE PROBLEM WITH MOST MATERIALS
Currently, the most common fibres used to make underwear are cotton and bamboo. The production of conventional cotton requires intense levels of chemical and water, with research showing that it takes 3kg of chemicals and 4,300 litres of water to make just 1kg of cotton.
Bamboo fibres are almost always produced through a viscose process involving a highly toxic substance, carbon disulfide. This chemical poses a health risk for both the people producing the fibre, and local communities through water pollution (eutrophication). We believe that these methods of production present too great a cost to our planet.
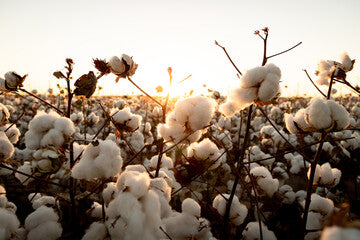
Organic & In-Conversion Cotton
Currently, only 1% of the cotton market is certified organic. When we use cotton, we always ensure that it is either certified organic or ‘in-conversion’. When farmers make the switch to organic practices, there’s a period of 3 years when the cotton they produce isn’t certified. This is what we call ‘in-conversion’ cotton. We believe using in-conversion cotton is even more impactful because it gives the farmers clear signals from the industry that making the switch is commercially viable, giving them confidence to make the change.
We're investing directly with farmers right now to create regenerative cotton ranges in the near future. We will be sharing our journey over the next year during cultivation and harvest, through to fibre and underwear production with full transparency of seed to product.
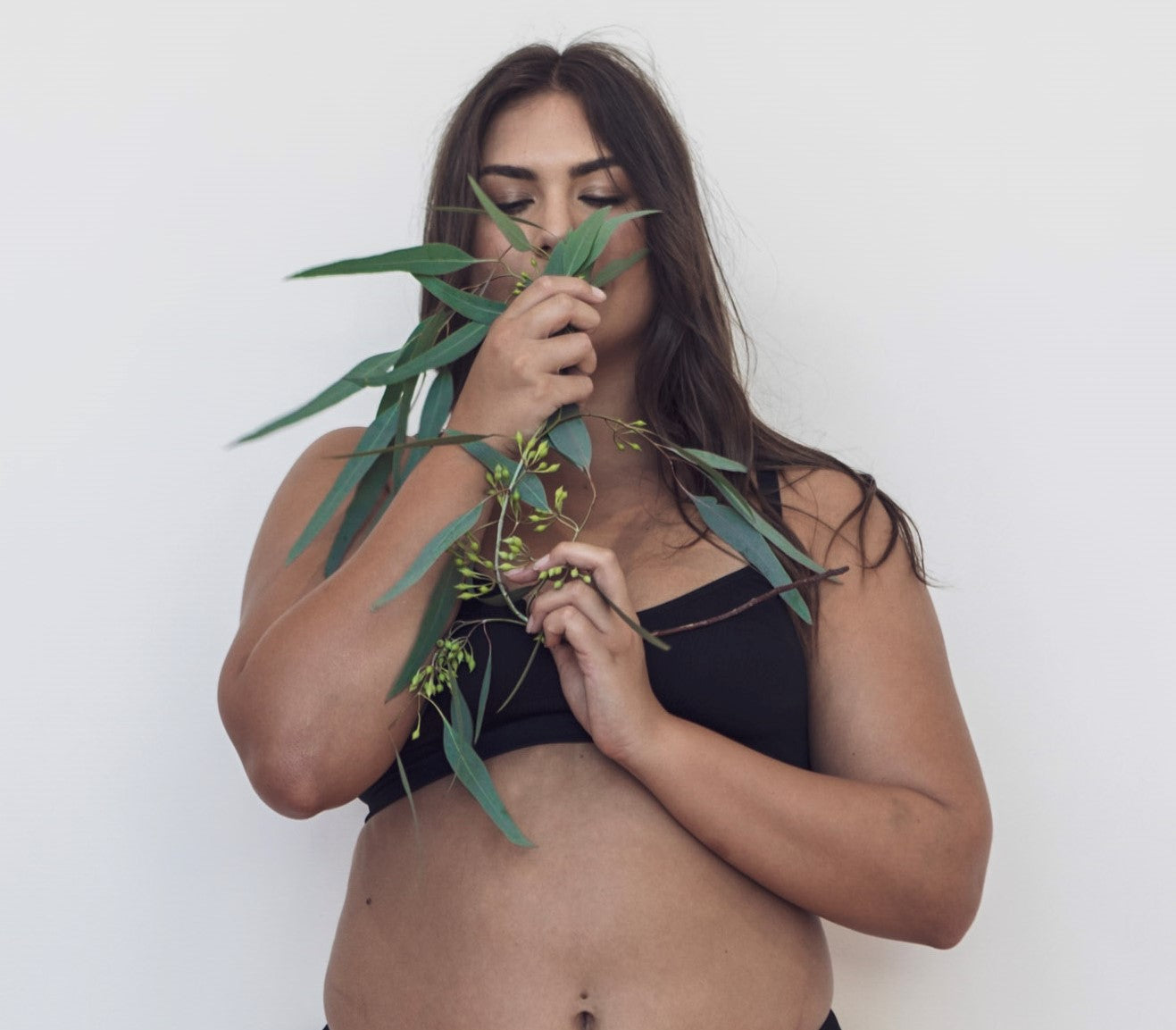
TENCEL
Instead of using bamboo, we have chosen to make our underwear with the sustainable and regenerated fibre, Tencel. Tencel, which is Lenzing’s brand name for the fibre process ‘lyocell’, is made using the wood pulp of certified Eucalyptus trees, meaning it is a renewable planetary resource. Eucalyptus trees are some of the fastest growing in the world, requiring no irrigation or fertilisers, and sequester carbon as they grow.
The ‘lyocell process’ (the method for turning wood pulp into Tencel fabric), is very different from a chemical perspective to the viscose process, it uses a safe surfactant in a closed-loop system, 99% of the water and solution are recovered and used over and over again. When released it is safe.
SEAM-FREE RECYCLED NYLON
We have chosen to develop our bras from recycled nylon and elastane seam-free tubes. Nylon is a synthetic fibre which is made from fossil fuels. There are so many synthetic fibres and plastics circulating in the fashion industry and so much industrial waste that needs adverting from landfill. The good news is, synthetic fibres are infinitely recyclable with no loss of performance, making them perfect for a circular economy. Our seam-free yarn is made from Global Recycle Standard (GRS) certified recycled nylon. This recycled nylon is created using repurposed industrial waste material, blended with elastane for extra support.
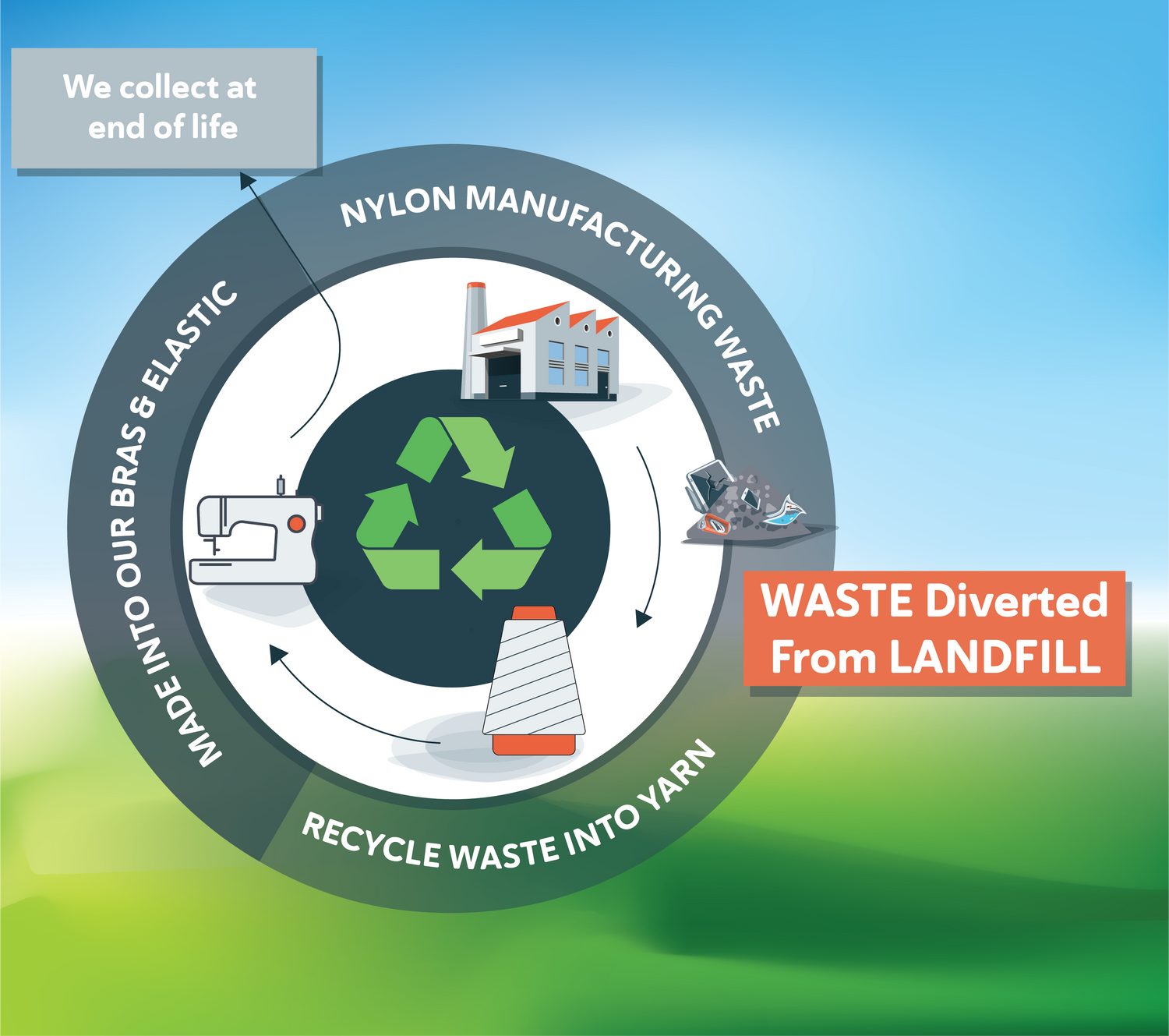
RECYCLED NYLON ELASTIC
Elastic needs to be soft and supportive to create a frame for underwear. It needs enough elongation to stretch and be comfortable to wear, but also enough power to hold.
While there are many suppliers of elastic, recycled elastic is very difficult to source, so we created our own. Our in-house elastic is a beautiful, soft elastic that is made from GRS certified recycled nylon.
The decision to use recycled nylon delayed our launch, but we were unwilling to use virgin nylon due to our uncompromising standards on the materials and processes that we use.
CHEMICALS IN PRODUCTION
The fashion industry currently uses over 8,000 chemicals in the processing and manufacturing of materials. Many of these chemicals are not even identified, let alone researched for safety. Of the ones that have been investigated, over 2,000 pose a significant threat to human health and are categorised as ‘substances of concern’. Due to decentralised supply chains, there is a lack of transparency in the fashion industry regarding chemical use and their full effects on the environment. To divert from these unsustainable and toxic chemical practices, we use Oeko-Tex certified dyehouses to ensure no toxic substances are used in the dying of our fabrics.